
If you are looking for a better place to work and live...
Join our team!
become an in-house tooling & mold maker
If experience and talent is what you have, then we want to talk to you!
Are you ready for good food, music, festivals, and the best hunting/fishing? Come and visit Lafayette, La in the heart of Cajun country. With our low cost of living and pleasant climate, why would you want to live anywhere else?
ASH Industries is a fast paced manufacturing company with almost NO 'same old same old' days of work. Engineers US-wide come to us with their designs (medical, industrial, consumer goods) and we use their prints, our ingenuity, plastic pellets, and chunks of metal to create finished injection molded thermoplastic products. ASH builds its own tooling & processes its own components. We have experienced consistent 6 to 12% growth/year beating back US & foreign competition. ASH is 27 years old, 60 employees, and we're NOT slowing down any time soon. ASH is NOT a micro-manage facility and we live by the “do your own thing, do it well'' credo. We work in clean, well-organized shop. Come for a visit and you will not want to leave.
OPPORTUNITY
· Qualified tool maker or machinist that can be trained into the art of mold building.
· Exciting opportunity to work on new projects weekly.
· Multiple production, experimental and prototype tools created each and every week.
• We are a full-service custom molder taking customers from design to the completed part. Our
in-house tool room builds tools from simple to the sophisticated
Tool makers are involved in an engaging variety of tasks from building molds, fixtures and related tools to completing tooling repairs and revisions.
RESPONSIBILITIES and DUTIES
· Build variety on components used in the injection molding industry.
· Aid in the development of faster more efficient machining and fixturing methods
· Provide input into the design and creation of molds and fixtures.
· Assist production molding department with some maintenance and troubleshooting duties
· Must be familiar with typical machining equipment like mills and lathes, grinders.
· Performs inspection for damage and minor repairs.
· Perform in press trouble shooting
· Analyze manufacturing feasibility and specifications using knowledge of tool design, shop math, and assembly procedures to re-build tools and dies.
· Works with little direction while performing maintenance on tools or fixtures for production
Ability to read tooling blueprints and/or engineering parts/welded prints, and work orders.
· Lead, direct, and guide others with a smile.
REQUIREMENTS
· 5 year experience in tooling and/or 10 years tight tolerance machining.
· Proactive, Self-starter / Motivated
· Able to read and interpret blueprints
· Tig welding a plus
· Injection molding experience preferred, alternate industry experience will be considered
BENEFITS
· Long term disability insurance
· Health Insurance
· Life Insurance
· Matching 401K to 3%
· 2 week vacation your first year in addition to 6 paid company holidays
· Reimbursement for educational advancement
Watch this video to see who we are...
Thermoplastic Injection Molding & Silicone Molding Parts Samples
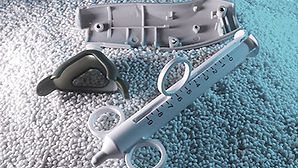
Custom Thermoplastic parts in complex or simple configurations for medical applications
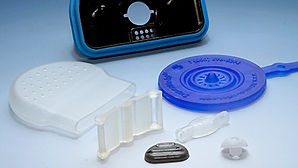
Silicone molding is available to produce flexible rubber parts that withstand harsh environments

We assist you with material selection based on your final use along with cost reduction suggestions
The ASH team will work to find the right combination of materials, part geometry, and quality testing to assure all components meet your exacting specs

Overmolding electronic parts help shield them from harsh environments and provides better life of the product
Partner with ASH Industries whose greatest advances have been in medical device molding forged from the most advanced materials

ASH specializes in medical devices and aeropsace Thermoplastic and Thermoset Silicone parts
We build your component with Design for Manufacturing and Assembly AND Design Failure Mode and Effects Analysis

Molded clear parts are defect free, functional and beautiful for medical and transportation industries

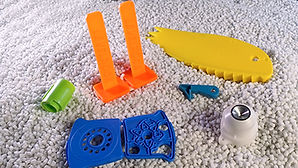

Specializing in Medical Injection Molding
ASH INDUSTRIES is an ISO 9001:2015 certified medical injection molding company with an ISO class 7 clean room.
We provide every option you need for the proper manufacture of medical devices, surgical instruments, durable or disposable medical products.
Since 1991, we have been supplying medical devices and assemblies to some of the biggest names in the healthcare industry.
ASH offers a wide range of capacity and press sizes that are state of the art. With injection molding presses ranging from 25 tons to 650 tons tons, no medical injection molding project is too big or too small.
Most of our plastic injection molding presses are equipped with high-speed, 3-Axis Robots for automated parts handling and inspection. Depending upon the volume of your medical injection molding project, ASH is equipped with manual or fully automated assembly equipment. If your product requires assembly, decorating, mechanical fasteners or special packaging, ASH has a plastic solution for you.
![]() | ![]() | ![]() | ![]() |
---|

SUPERMOLD - Production Tooling with a lifetime guarantee
From purchase order to first article in 3 weeks in most cases. Spend “prototype dollars” on production molds designed to take advantage of production efficiencies within ASH Industries. SuperMold™ reduces costs and lead times for custom injection molds to process thermoplastic, silicone, or MIM components.
At the same cost to you as a prototype mold, SuperMold™ uses tool steel to provide a production mold that is guaranteed for as long as you need parts. Our full tool shop allows quick turnaround to put parts in your hand when you need them.
At ASH THERMOPLASTIC INJECTION MOLDING manufacturing group within ASH Industries™, our list of projects span a wide gamut of industries and OEM projects. From medical surgical devices to structural components for laser light shows to overmolded electronic components, we can do it for you. We understand FDA or FAA requirements so you know that you are working with experience in injection molding and thermoplastic molding.
All of the project engineers you will work with have one thing in common, they all seek solutions to production questions. Customers also benefit from ASH's implementation of JIT and TOC programs to limit inventories for production runs of ten million assemblies to a thousand custom parts.
Engineers at ASH Industries understand the complexities of beginning a new project and will work to ease that transition. We will ask a lot of questions and will help you with the tooling to make the best parts at the best price.
PROS OF INJECTION MOLDING: Every production process has it's pros and cons. Here are some of the advantages of thermoplastic injection molding:
Accuracy: Thermoplastic injection molded parts are able to be produced with pin-point accuracy, which is a major advantage over other prototyping processes like 3D printing.
Surface Finish: Thermoplastic injection molding can be executed with a variety of general and engineering-grade resins. The process is also able to create parts with pristine surface finishes, which makes the production process viable to create not only prototypes, but small and large production runs. Rough or pebble textured surface finishes can also be created with the production process.
Speed: Parts that are thermoplastic injection molded are typically turned around within days. If it's used for prototyping, this allows developers to make design changes quickly, thereby enabling it to go to market sooner. And if the process is being used for manufacturing, runs can be completed within days, so they're able to be on store shelves sooner. The longest part of the injection molding process is the time that needs to be spent creating the mold. However, molds can also be created to fine-tune prototypes and then used again for a manufacturing run.
Predictor of manufacturability: Thermoplastic injection molding can be utilized for prototyping purposes. Parts can be completed and turned around quickly with in days, with accuracy and surface finish quality. This makes the process a great predictor of manufacturability. Often times, developers will order several early prototyping runs on other technology, then use thermoplastic injection molding to validate product design prior to green-lighting the product for manufacturing. Since parts can be crafted in several different resins, developers will also experiment with surface finishes and materials to see what material they want to use.
APPLY
Upload Resume
